GMT-3D
October 2024
GMT-3D
GMT-3D is a project launched in collaboration with the University of Catania, within the SAMOTHRACE ecosystem and funded by the European Union - NextgenerationEU.
SAMOTHRACE aims to realize the vision of a global collaborative environment among key players in the field of microelectronics, microsystems, materials and microtechnologies operating based in the Sicilian region but with a global perspective.
SAMOTHRACE focuses on the European Commission's global challenge - Digital, Industry and Space - but also addresses other challenges such as Health, Energy and Mobility, Agriculture and Environment.
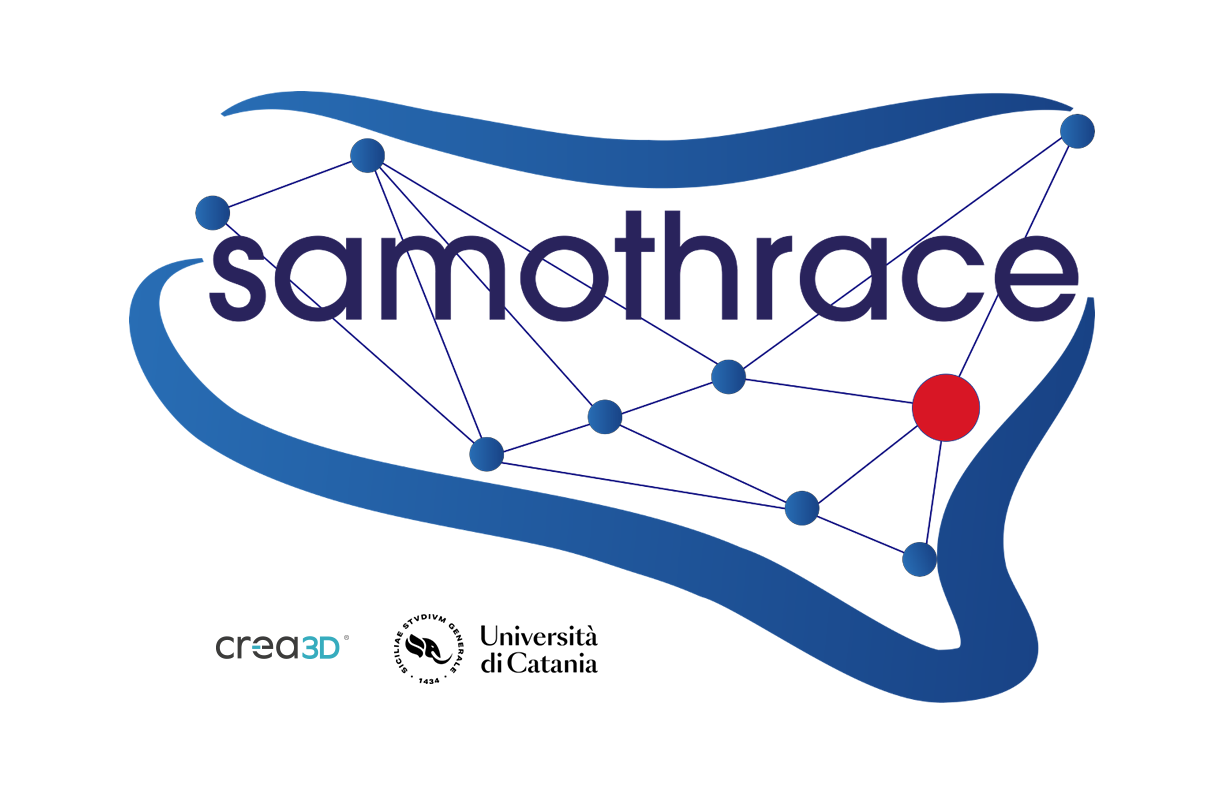
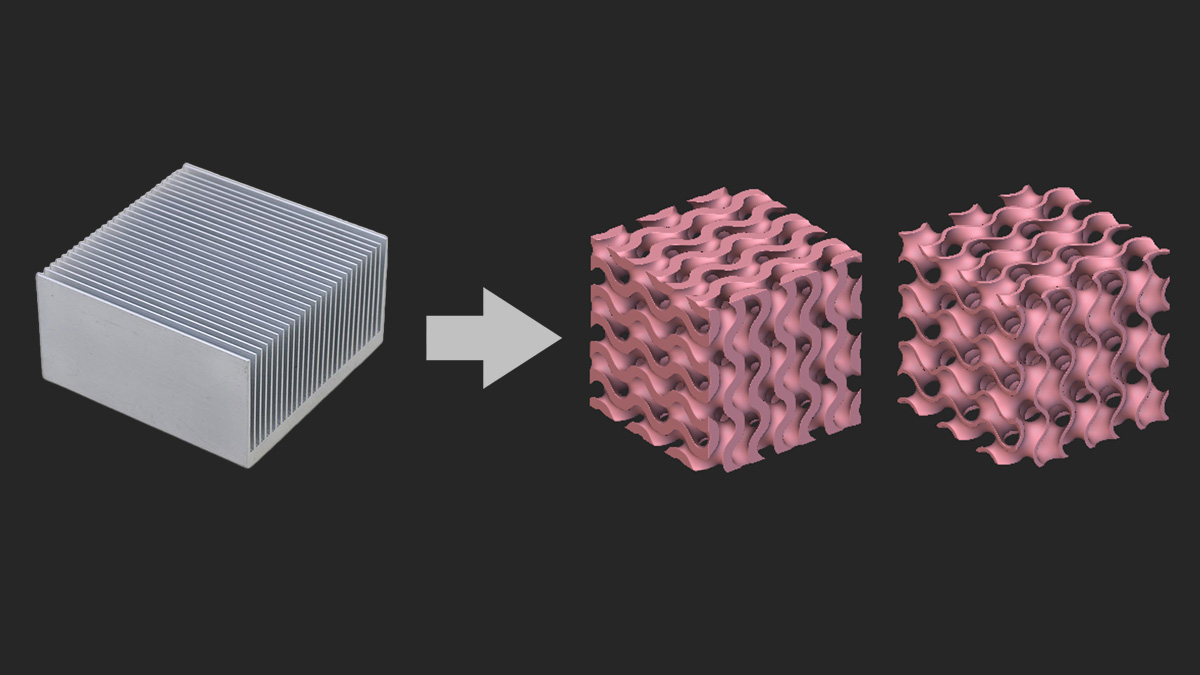
The new dimension of 3D cooling
GyroidMax Thermal (GMT-3D) aims to produce highly efficient heat sinks using advanced Additive Manufacturing (AM) technologies.
This design exploits the geometric complexity of gyroid and SplitP structures to optimize heat exchange, incorporating innovative materials such as copper, AlSi10Mg aluminum alloy, 316L stainless steel and 17-4 PH stainless steel.
The project integrates advanced scientific considerations, including thermo-fluid dynamics and the influence of surface roughness, based on recent studies and CFD models.
Goals
- Geometric Optimization: Develop heat sinks with gyroid and SplitP geometries, capable of maximizing the surface/volume ratio for effective heat dissipation.
- Materials Research: Evaluate the thermal and mechanical properties of copper, aluminum, 316L and 17-4 PH stainless steel, with a focus on thermal conductivity and mechanical strength.
- Thermo-Fluid Analysis: Examine the effect of surface roughness on thermo-fluid dynamic parameters, such as pressure drop and heat transfer, using advanced CFD simulations and theoretical models.
- Prototyping: Build prototypes using MFFF, EBM and SLM technologies, and test them to evaluate thermal efficiency and feasibility of large-scale production.
- Sustainability: Implement sustainable manufacturing practices, aimed at reducing CO2 emissions and material waste.
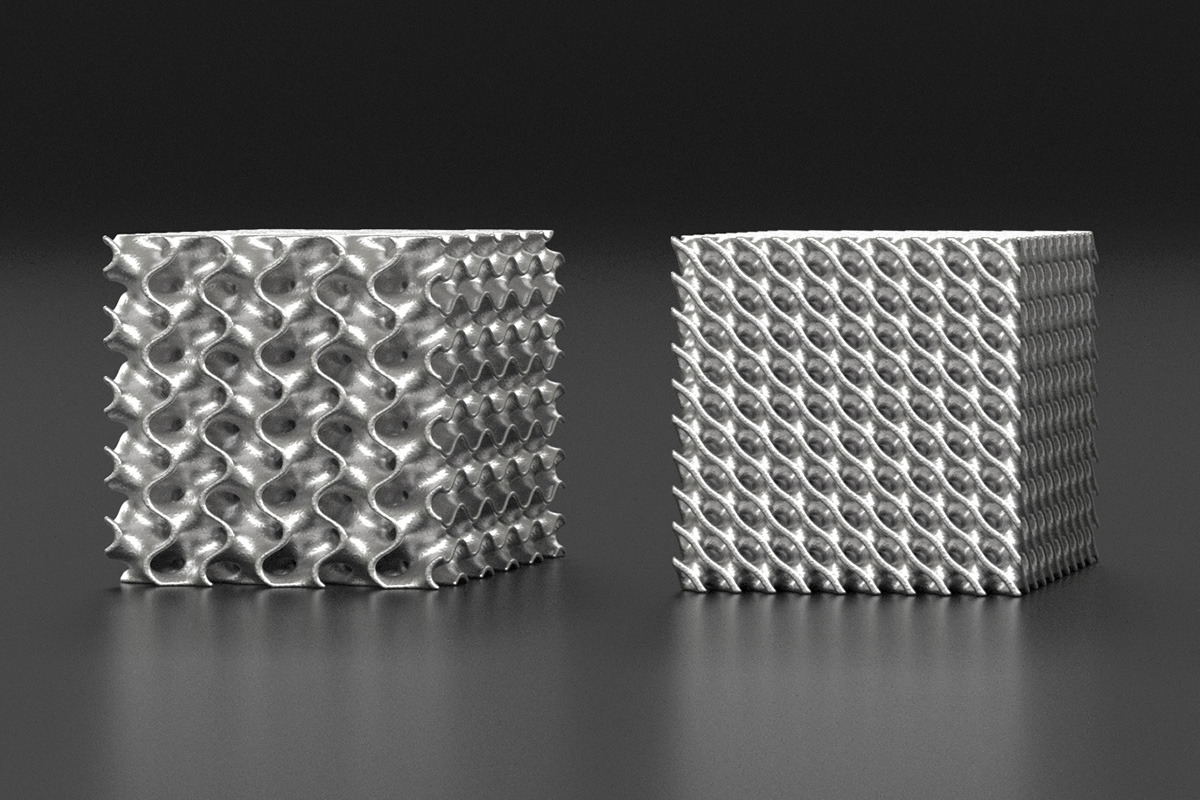
Testing Methods
- Analysis of gyroid and SplitP geometries using advanced software such as nTop and Ansys Fluent.
- CFD considerations: sand-grain roughness model in Ansys Fluent to simulate the influence of roughness on fluid dynamics and thermal distribution.
- Additive manufacturing techniques:
- MFFF (Metal Fused Filament Fabrication) for rapid testing and iterative prototyping.
- EBM (Electron Beam Melting) and SLM (Selective Laser Melting) for prototypes with high dimensional precision and excellent mechanical properties.
- Thermal Efficiency Testing at operating temperatures between 175-200°C, followed by a cooling cycle in air and in refrigerant fluids such as water and glycol.
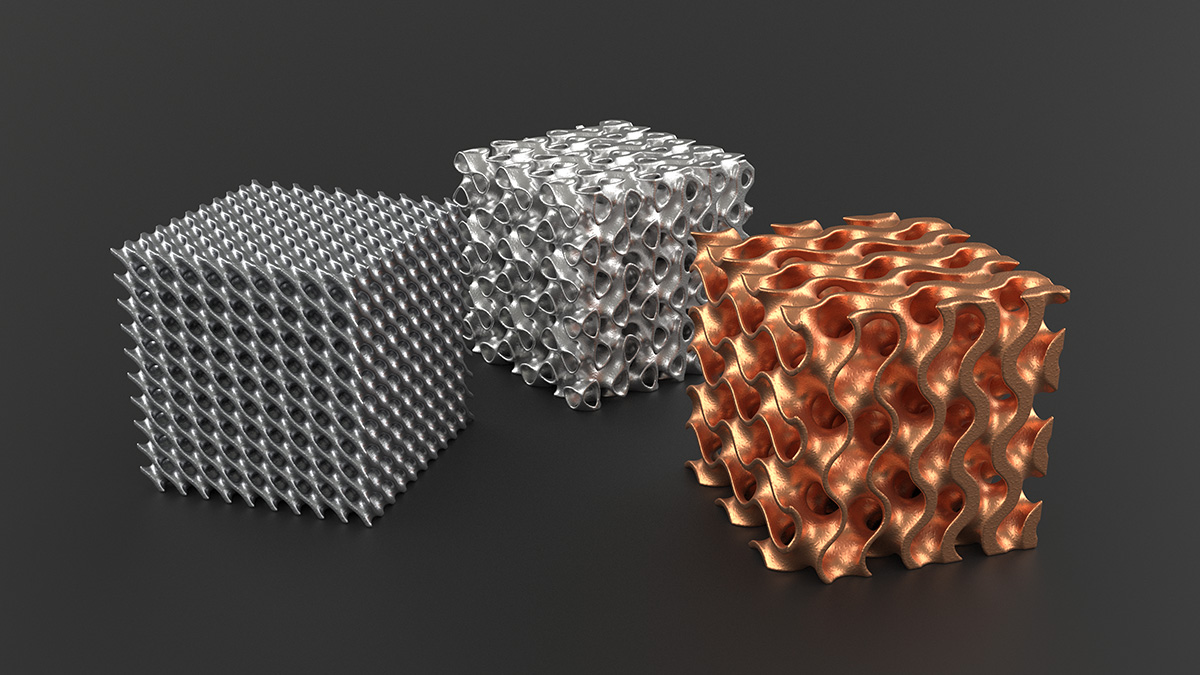
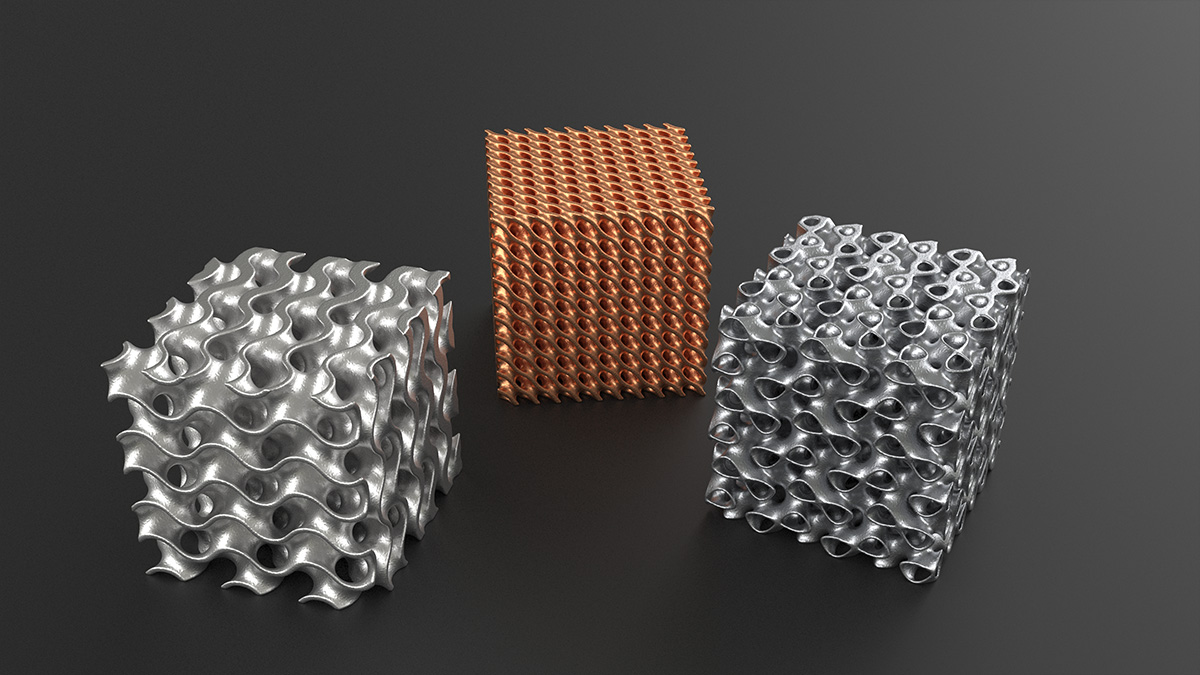
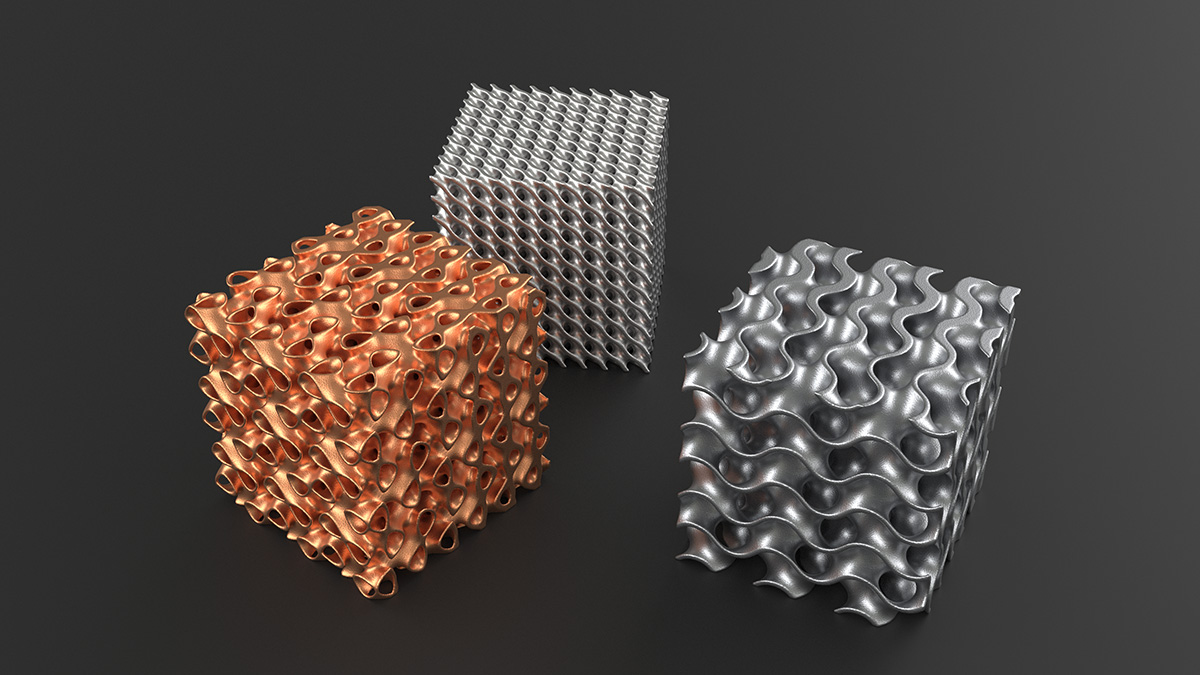
Timeline
AUG-OCT 2024
Phase 1: Research and Development
AUG-OCT 2024
NOV 2024 - JAN 2025
Phase 2: Prototyping
FEB-APR 2025
Phase 3: Optimization and Testing
FEB-APR 2025
MAY-JUL 2025
Phase 4: Production Scalability